
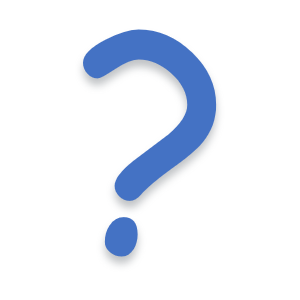
DOH, skipped those two critical letters! Thanks for the correction.
DOH, skipped those two critical letters! Thanks for the correction.
Astronomers already use Julian Dates for various reasons. Right now it’s 2460261.2834606, it’ll be later by the time you read this. Julian dates/times are fractional days starting from January 1st, 4713 B.C. = 0. Just keep counting up from there.
Budgerigars (small parrots).
They’re active, smart, and social. They fly.
So I made them a flight cage that takes up most of the room they’re in. I’d prefer a full walk-in aviary, but don’t have room in my apartment.
Cleaning isn’t bad, I just shop-vac out the litter tray & refill it with a 20lb bag of corn cob bits. Fresh food in the mornings, take it out & replace with pellets around noon. Clean water daily. Millet treats when I let them out (about an hour per day to interact with them).
Feathers get everywhere when they molt. And feather dust. Their room has its own HEPA filter.
Vet appointments are more expensive for exotics than cats & dogs. There are fewer exotic vets, and I always go to a board certified avian vet. Boarding when I go on vacation is also more expensive (about $50/day), especially since they’re flighted.
They’re not anywhere near as loud or destructive as larger parrots, but that doesn’t mean they’re quiet. Just means they might not damage your hearing from the next room. They wake up with the dawn, and let you know about it.
They’re extremely sensitive to airborne toxins (avian respiration is rather different from mammalian). That means absolutely no teflon cookware use, no air fresheners, etc.
Plan 9 From Outer Space.
Or anything Ed Wood directed, really.
__auto_type
is a compiler builtin, not a library function. It’s not a function at all, the parentheses are for precedence & grouping.
#define max(x,y) ( { __auto_type __x = (x); __auto_type __y = (y); __x > __y ? __x : __y; })
GNU C. Also works with Clang. Avoids evaluating the arguments multiple times. The optimizer will convert the branch into a conditional move, if it doesn’t I’d replace the ternary with the “bit hacker 2” version.
Worth trying. It’s already broken, you can’t really make it much worse. It’d probably work, and worst case you’re back where you started & paying for expensive shipping.
Copper or silver-based should be lower resistance. These conductive paints tend not to be very conductive, the carbon stuff is essentially making a thin-film carbon composition resistor. Good for repairing rear window defroster heating elements, not so great as a 0-ohm trace in a keyboard. For short (<1cm) wires it’s usually not too bad, but with the amount of damage I’m not sure you’ll be able to repair the thing.
It looks like it might be from a Model M-style keyboard. Unicomp sells those.
You mean SNI, not ESNI. ESNI is the Encrypted Server Name Indication that gets around that, though the newer ECH (Encrypted Client Hello) is better in many ways. Not all sites support either though.
We’ve had open-source chip design software since the 1980s. Magic VLSI, for example. There are quite a few OSS tools for various parts of the chip design process.
Also bleeding-edge processes mean smaller, thinner gates. That’s what gives them the fast switching speeds, but it reduces the max allowable voltage. For parts that need to handle more than 1.8V or so a modern 5nm process will just end up using bigger gates than the process is optimized for. May as well go with an older process (bigger minimum gate size) that’s better suited to switching the voltage needed. For Bosch (automotive parts, power tools, etc) they’re making a lot of parts with really big output transistors (switching 14V, 48V, etc) and not super high-performance processors.
The big disadvantage with particularly old processes is that they used smaller wafers. So fewer chips per wafer processed, meaning lower overall yields and higher price/chip. The switch from 200mm wafers to 300mm in 1999 meant the wafer area increased by a factor of 2.25! 300mm wafers also required fully-automated factories due to the weight of a wafer carrier (a front opening wafer pod, or FOUP, is 7-9kg when loaded with 25 wafers), which save on labor costs. So processes older than 1999 (around the 180nm node) are sometimes not worth it even for power electronics.
You don’t have an autoformatter in your pre-commit hook? Why not?
That is an excellent source.
Looks a heck of a lot like the RS-485 serial cable I’ve got on my desk right now. Scale is hard to tell, not sure how big that bowl is.
Soylent green, clearly.
Or meat. Humans are mostly meat.
Many cameras these days have AI autofocus for subject detection. Phone cameras use AI image enhancemnnt by default.
And color management. Useless for photo editing, stuck with 8-bit sRGB.
Same, I’ve tiny hands and a Note 9. Works fine.
If GitHub’s UI isn’t saying “infinity files changed” you’re not trying hard enough.
Not much coverage of Vermont’s senators? Did you miss all the Bernie Sanders coverage even when he’s not running for president?